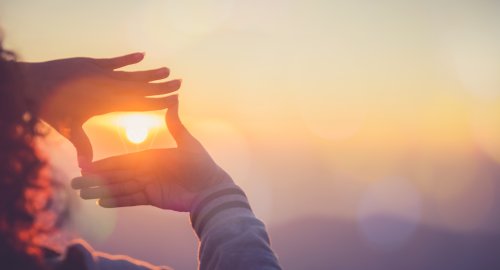
Listen to Engineering Angles, Tractebel's podcast!
In the latest episode of Engineering Angles, we caught up with Neha Bansal, Deputy General Manager of Hydropower & Water Resources in Business Development &...
Lees verderDid you know that 80% of diesel consumption in open-pit mines is by trucks? Each of the 1,000+ mines worldwide generates 120 kilotons of CO2 annually from transport alone. Our Tractebel experts helped develop the hydrogen value chain to power the first-ever emissions-free mining truck.
The world’s first hydrogen-powered mining truck fired up its engine at the Mogalakwena mine in South Africa, the largest open-pit platinum mine in the world. As mining companies across the globe seek ways to cut their carbon emissions, global mining giant Anglo American is developing this remarkably innovative solution to use hydrogen as fuel to decarbonize their mining activities. ENGIE developed the hydrogen value chain for this proof-of-concept truck, that singlehandedly can eliminate eight tons of greenhouse gas emissions each day.
The potential of hydrogen-powered mining transport and extraction trucks in the fight against climate change is astonishing.
The world's first hydrogen-powered mining truck, capable of eliminating eight tons of greenhouse gas emissions each day
Tractebel sets the course for the first hydrogen-powered mining truck
Tractebel has been involved in this mining transport decarbonization initiative from the start. Our hydrogen experts contributed to the concept’s development phase and pre-feasibility studies in 2018. We began finalizing the technical concept in 2019, and were named Engineering, Procurement and Construction Management (EPCM) contractor by ENGIE later that year.
The Tractebel project consists of producing hydrogen using a 3.5 MW electrolyser to split the water molecules (H2O) into oxygen (O) and high-purity hydrogen (H2), to be used for the fuel cells installed on the mining truck (beyond Tractebel’s scope). To achieve this, raw water is treated and demineralized, then sent through the electrolyser. High voltage AC/DC rectifiers provide the required energy for the conversion. As a result, pure hydrogen is produced. It is stored at high pressure (500 bar), ready for consumption.
Tractebel teams on-site at the Mogalakwena mine in South Africa
Cross-border collaboration drives decarbonization
Our EPCM mission includes multi-package tendering, design review, and construction and commissioning supervision of the proof-of-concept (POC). We developed protocols and an optimization strategy for heavy-duty refuelling, and flexible internal transportation technology. Our experts are also ensuring preliminary business modelling, which involves defining, sizing and optimizing the entire renewable hydrogen supply chain and supporting the client on the scale-up project value. The team from Belgium collaborated with our colleagues from India and South Africa on design and for local expertise, respectively.
The hydrogen electrolyzer building designed by Tractebel
Tractebel supported development of the hydrogen value chain to power emissions-free mining trucks
Shifting gears in the fight against climate change
Each truck, capable of carrying 290 tons, currently burns roughly 3,000 litres of diesel fuel and emits eight tons of CO2 emissions each day. The climate change mitigation potential of hydrogen-converted mining trucks is staggering: if the 1,000+ open-pit mines worldwide switched to hydrogen-fuelled trucks, a colossal 120,000 kilotons of emissions would be eliminated from the atmosphere each year.
But before we are there, this prototype project is currently demonstrating its reliability and performances to provide sufficient confidence in scaling up towards a jump into the green era of mining-trucks.
“Decarbonizing mining is a huge step towards reducing emissions on a global scale, and developing hydrogen-powered mining trucks is a quantum leap towards that goal. We all use products derived from mining in our daily lives, so the reality is that it’s essential. But we need decarbonize it. It was an honour for our teams to contribute to a project – a world first - with such far-reaching consequences for a carbon-neutral future.”
Johan Claeys, Tractebel Project Management Leader - Green Fuels
In the latest episode of Engineering Angles, we caught up with Neha Bansal, Deputy General Manager of Hydropower & Water Resources in Business Development &...
Lees verderTractebel helps ENGIE build its second large-scale battery park in Belgium, contributing to shaping a flexible, reliable and sustainable energy system in the country.
Lees verderOur Urban teams from France and Monaco are leading the design and construction supervision of the Mediterranean Pavilion, ahead of the third United Nations Ocean...
Lees verderOur transport infrastructure experts signed a mandate on April 25, 2025, to provide technical services on the first metro project in the Western Balkans. This is our...
Lees verder